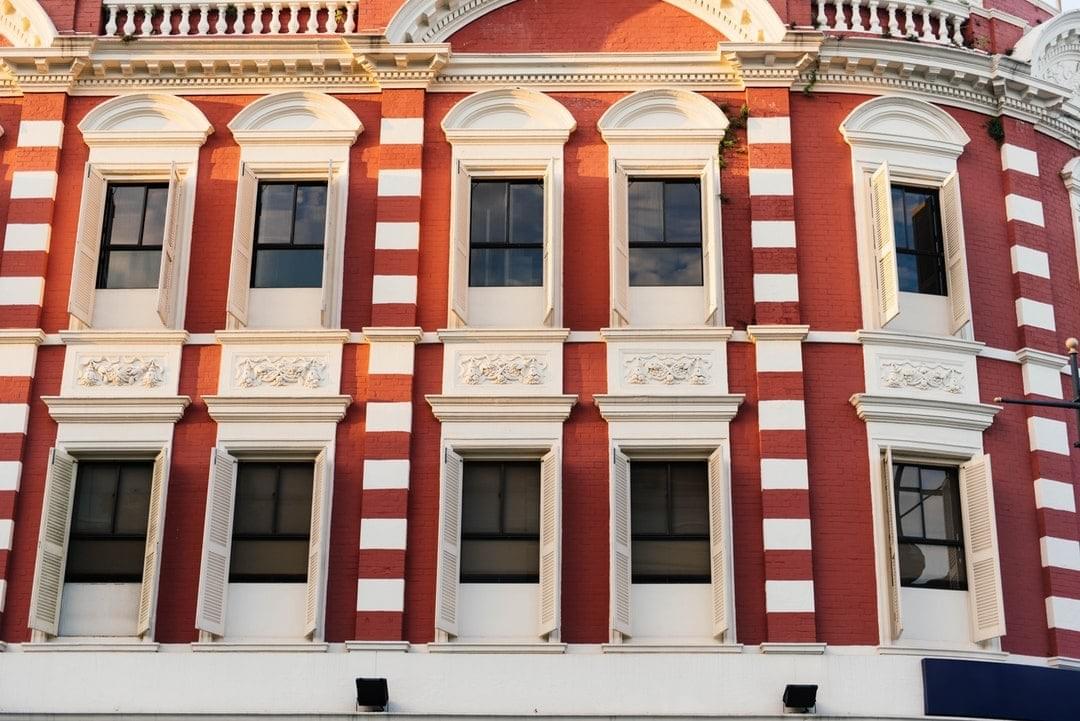
Several manufacturers are now using overmold as they embrace the fact that their product line values are being increased. It improves the performance, functionality, and aesthetics and lowers the costs of production which is not common today. Overmolding is a procedure of one or two shot that attaches a lean layer of thermoplastic elastomer to the product’s substrate . This external layer forms the popular soft-touch grasp for many products ranges like individual care items such as toothbrushes and power tools. Overmolding further lowers vibration and shock, inhibits sound, offers electrical protection, aids resistance to UV or chemicals, and even hinders moisture and oxygen.
Subsequently, more buyers are requesting this touch to the items they buy hence the expansion of Cavist overmolding applications. Product engineers are given many chances by this technology availability the ability to form functional and attractive items that stay continuously on the markets leading edge. For successful production run, not all injection-molders can overmold but they need specialized training, state of the art equipment and proper control of several variables. Even the scarcest varieties can influence quality, so qualified operators are an absolute necessity. A lot of this know-how is connected to the products being utilized therefore a deep knowledge of chemical behavior and material science is needed. There is continuous engineering of new paint mixes to give properties that are expanded like clarity, hardness and resistance to heat, chemical, UV and scratch.
The main aspect of overmolding is evaluating the combination for substrate and for bonding, and coming up with the right tools and molds. It is important to keep the melt temperature because it affecting the flows and bonding. The surface of the substrate should be clean with no skin oil, dirt, excessive moisture and dust contaminations so one should put on gloves when handling so that they may be strong. For more facts and information about molding, go to https://en.wikipedia.org/wiki/Plastics_engineering.
Vents should be placed in the mold and properly sized to allow the air release from the mold cavity when overmolding. It is uncommon in case there is improvement through advance technology a products viability and gain client satisfaction and also lower the production cost. The costs go low if overmolding is able to reduce the steps followed in the production. Viscosity, flow rate, material type, and shear amount may be needed for deciding the gate size. When the steps are followed the procedure of one injection, the molding quality helps in throughput, waste reduction and reduced the cost of production. On shutoff for proper designs the involved materials to curling and risk of delamination. Know about lpm services here!